IML goes Medical: Why In-Mould-Labeling can become a game changer in the medical technology
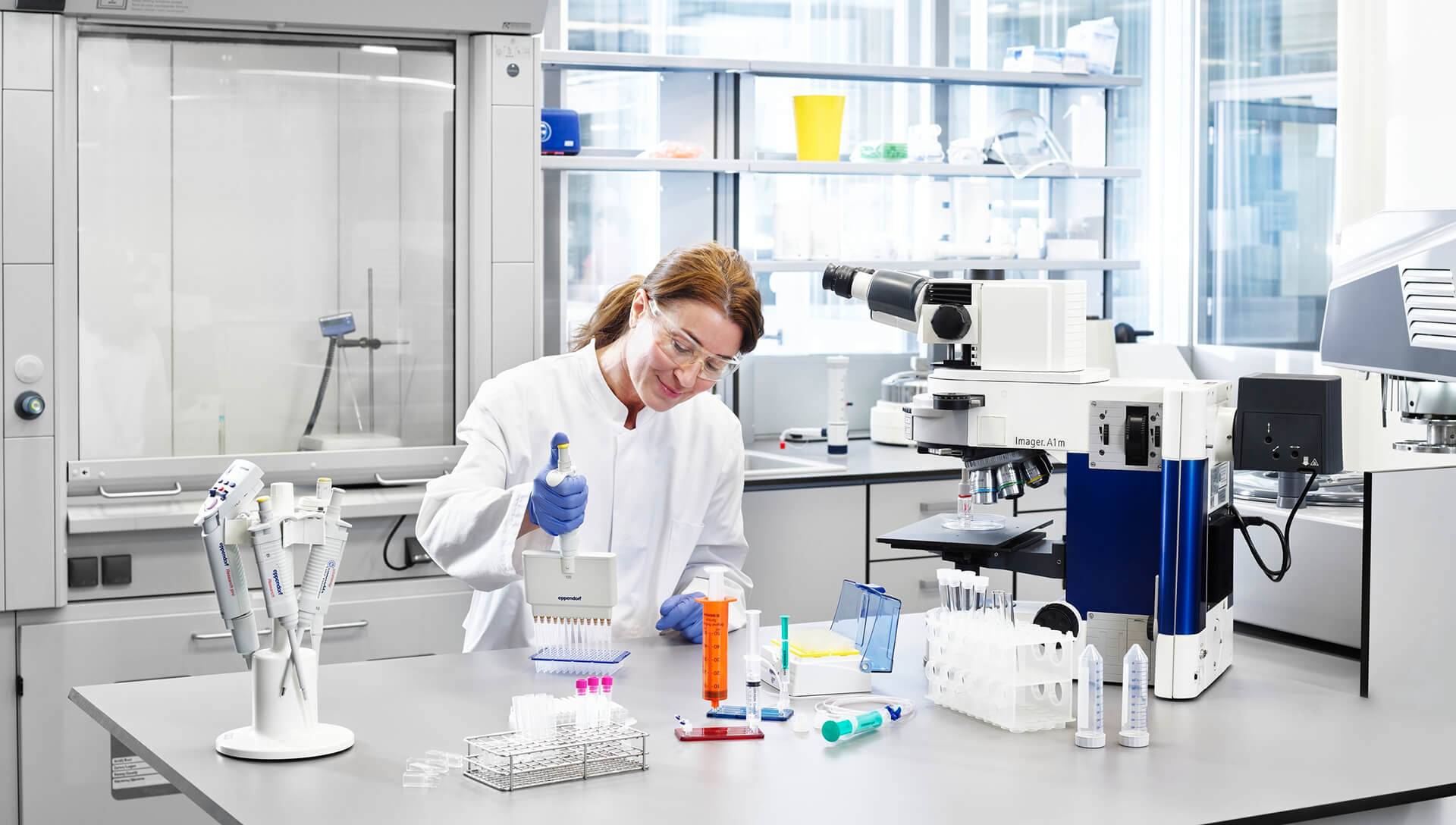
In-Mould-Labeling (IML) is familiar from packaging and is now state-of-the-art. Five partners are developing an IML concept for medical technology. Will this bring about a change in technology?
There is great interest in the new technology on the part of the industry, as additional functions can be integrated into the plastic part. These „add-on functions“ are interesting for the pharmaceutical and medical industry because they open up new potential benefits and markets. The global medical market is changing: new consumer segments are emerging, but also new players (increasingly from the technology sector).
„When it comes to new products, creativity and experience count,“ reports Johannes Strassner, CSO at KEBO. With long-standing partners, the idea was born to jointly develop the topic of IML Medical as a team. Arburg, Beck Automation, KEBO, MCC Verstraete and Intravis worked together on the concept.
Reduce risk and avoid mistakes
The safe use of products and the exclusion of incorrect manipulation are of elementary importance in medical technology. This includes all products in pharmaceuticals, medical and laboratory diagnostics for various forms of application and administration. The IML process produces a finished part in a single-stage process, thus reducing (end-to-end) manufacturing costs.
Unlike many current manufacturing processes, IML guarantees a safe product. Self-adhesive labels can be peeled off or replaced, while authenticity can be safely guaranteed via IML. IML of the latest generation, in conjunction with intelligent downstream systems, maps the complete manufacturing process of a product. This eliminates the need for scrap-sensitive decoration processes such as printing. The logistical and space requirements are reduced, as is the risk of contamination.
Label ensures digital traceability
Particularly in the medical industry, connectivity and traceability will be essential. Digitization opens up new possibilities, for example in doctor-patient communication and in the traceability of supply chains for medical products. IML ensures efficiency and safe use through unique coding on the label. Kim Blondeel, business development manager at MCC Verstraete, reports that the latest generation IML enables innovative features such as temperature indicators and additional functions such as serialization with unique coding. In addition, RFID applications are part of the development.
Keeping an eye on recyclability
In the medical industry, topics such as sustainability and recyclability are important factors in product development and are incorporated into the process at an early stage. As early as the concept phase of a new product, the marketer addresses issues related to the reuse of raw materials. For products manufactured with IML, both the label and the carrier are made of the same plastic. This allows for joint disposal and easy recycling. However, the focus is also on fundamentally reducing the amount of material used. In this context, labels can have a stabilizing effect, wall thicknesses can be reduced and material can be saved - all while maintaining the same product quality and properties.
Economical and hygienic at the same time
The integration of different processes in one system eliminates unnecessary transport and further processing steps, which minimizes the risk of unhygienic influencing factors. Among other things, products manufactured by IML are less susceptible to microbiological contamination. Medical production areas require a high level of investment, as specific standards and specifications must be taken into account when setting them up and equipping them. If production has to take place in a clean room, costs rise even further. Thus, there is a great interest in being able to use this production area as efficiently as possible. Machines that enable a wide range of processes in a small space, meet the requirements of cleanroom class ISO 7 and require little service and maintenance are elementary in this respect. The common goal of all technology partners is a production system with a low footprint and high productivity.
Medical and pharmaceutical products require the highest precision to enable low-risk, accurate application. The manufacture of medical devices and consumables is highly regulated and must meet the highest requirements. New functions require safe and flexible technologies. For applications with high precision requirements, partners rely on a combination of high-precision labels, their exact positioning and optical inspection systems. Functional elements such as scales or components such as an RFID chip are placed on the product with repeatable accuracy. Optical inspection systems provide process-relevant data, detect trends, and ensure minimal waste through early intervention.