Part 5: One vision for almost 30 years
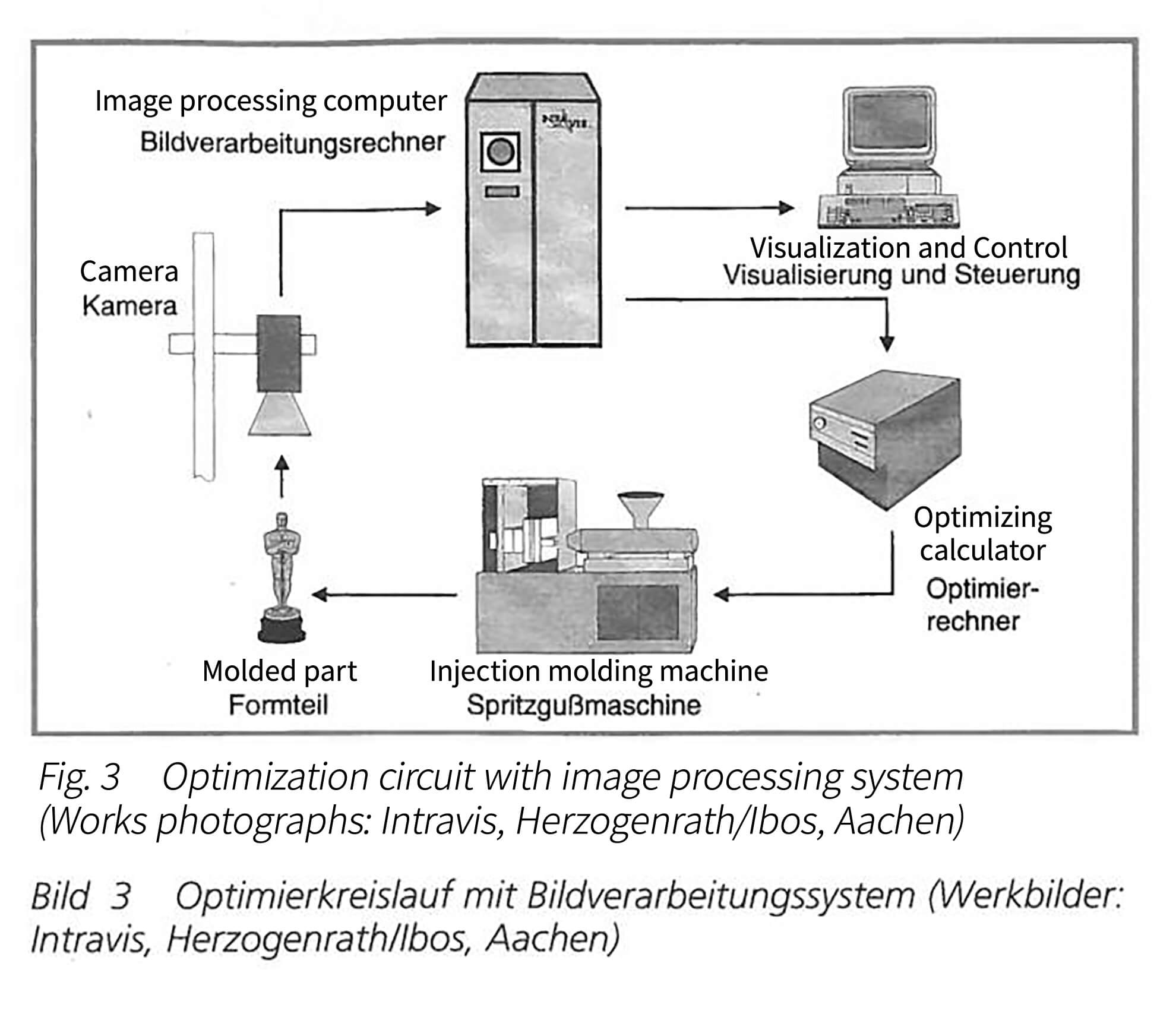
On the occasion of our 30th company anniversary, we look back on the development of INTRAVIS in a 6-part series. We shed light on where it all began, why INTRAVIS is actually called INTRAVIS, what influence a student had on our start in the plastic packaging industry, and how a vision has always driven us for 30 years now. Today: Through the years, we have developed many different systems and technologies. Some of them have accompanied us for more than 25 years.
"We solve problems. Before they occur." This has been the official vision of INTRAVIS since 2016. In fact, however, we have been pursuing this vision since 1996.
But first: What does the vision actually mean? "Our vision aims to ensure that the data collected by our inspection systems helps our customers to keep their production processes and delivery quality stable and optimized. With the help of this data, problems are then avoided that would otherwise have come to the manufacturer in the near or middle future," says Markus Juppe, Chief Marketing Officer at INTRAVIS.
And INTRAVIS has been pursuing this vision since 1996? Yes, indeed! Back then, we already published an article in the German industry magazine Plastverarbeiter describing this on the basis of a closed control loop. In this closed loop, the processes and thus the product quality are constantly stabilized and improved on the basis of the most recently collected quality data - and this completely automatically.
In concrete terms, this means that as soon as an inspection system detects that a quality parameter of a product exceeds a limit range, it reports this back to the manufacturing machine. The machine then also makes fully automatic changes to the manufacturing process so that the next product is again produced within all tolerances.
That was the theory. "In practice, we were way ahead of our time with this idea," reports Dr. Gerd Fuhrmann, CEO of INTRAVIS. "The computing power of the PCs at the time quickly reached its limits with this project, so we were initially unable to implement the idea as we had imagined. However, we were able to do the right preliminary work by developing our systems more and more so that they collected extensive product quality data and did not just sort out bad parts, as was the industry standard at the time." That's why INTRAVIS systems have always been equipped with extensive statistics, defect image memories, or even alarm messages, and to this day bring added value to operators with their comprehensive information, leading to increased efficiency at the end.
In 2015, we then took a new approach to implementing a self-regulating control loop. Systems like the then CapWatcher III were now delivering huge amounts of quality data per minute. In addition, the computing power of industrial PCs had increased many times over since 1996, so we now had the most important basic components available. All we needed was the right software.
We therefore developed the IntraVisualizer, a data analysis software that combines and analyzes the quality data of several INTRAVIS systems, forecasts trends, and visualizes the results in a comprehensible way.
The combination of this software and the data from the CapWatcher III could be admired at Drinktec 2017 in a closed control loop implemented for the first time with a Netstal injection molding machine. In this case, parameters of the injection molding machine were specifically changed in such a way that closures were produced outside the tolerance limits. The CapWatcher III detected this and reported its results back to the injection molding machine - as a result, the relevant parameters could be adjusted so that the closures were again within the tolerance limits. The demonstration of a closed control loop.
And what has happened since then? "Quite a lot," reports Wolfgang Jansen, our Chief Development Officer. "We are working wholeheartedly on further products that will enable line operators to solve production problems independently and minimize machine downtimes on the basis of empirical values and machine data."
Industry is also increasingly seeing the need for such solutions. Markus Juppe says: "Production lines today are incredibly complex. Line managers have several production lines with countless different machines and systems under their responsibility. To make it easier for these line managers to do a good job, companies are willing to invest in the automation of their production lines - also thanks to the increasing networking within the framework of Industry 4.0. Because in this way, they simultaneously also ensure a high level of efficiency with consistently high quality for the future."
Thus, the vision that originated in 1996 is still an essential topic in the industry today, which we continue to pursue with all our might.
In the last episode of our series, we take a look behind the scenes as a few employees from different departments talk about their work at INTRAVIS.
Click here for the previous articles in the series:
- Part 1: The beginnings of INTRAVIS
- Part 2: How we moved to plastic packaging
- Part 3: We grow!
- Part 4: About bottles, closures, labels and preforms