Successful Commissioning in Slovenia - SpotWatcher Customized shows its strengths
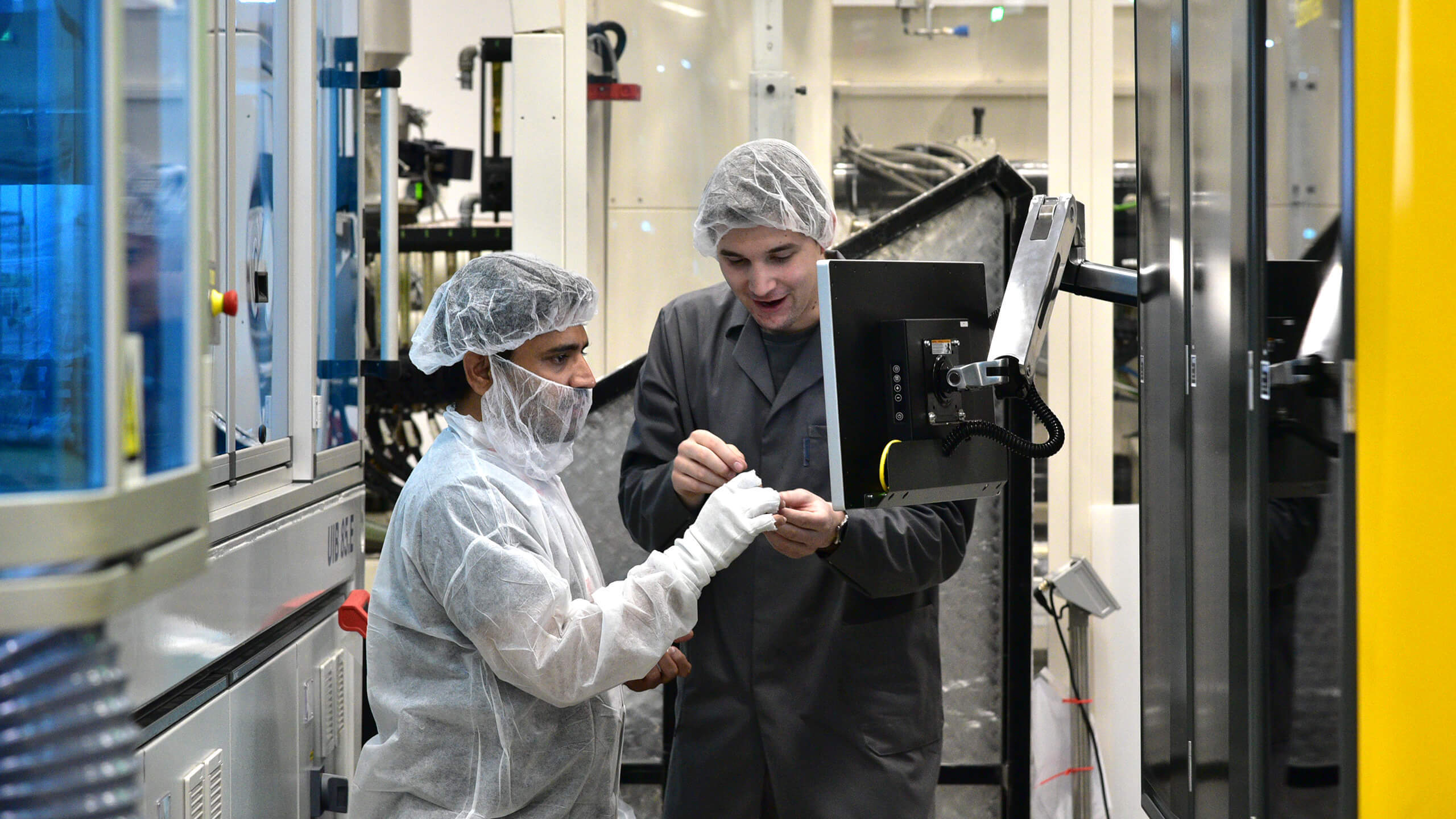
What distinguishes the SpotWatcher Customized, our tailor-made inspection system for the inspection of bottles and containers? Why do producers of plastic packaging repeatedly opt for this INTRAVIS solution for quality assurance?
The answer to this question is as simple as it is clear. Like no other system, the SpotWatcher Customized stands for a wide range of proven inspection solutions to deal with the broad spectrum of possible sources of error in the production of plastic bottles. The high level of innovation and rapid integration of new convenience, design and safety features is also well known, not least from the blog posts on this page. The system can therefore meet almost any customer requirement and enable maximum inspection quality. If no compromises are to be made in terms of product quality and safety, there is often no way around a SpotWatcher Customized.
The SpotWatcher was recently able to prove this once again and convince the Sibo Group from Slovenia of its advantages. As a producer of small to medium-sized pharmaceutical containers, the Sibo Group's top priorities are product integrity and maximum quality. This applies equally to opaque, translucent and transparent containers. In consultation with the customer, we were able to develop a customized solution. In March of this year, the time had finally come. The SpotWatcher went into operation in Skofja Loka.
Every container produced is now thoroughly inspected here. The outer walls, the thread and the side contour are checked in a 360-degree inspection for contamination, holes and burns as well as various types of shape deviations (e.g. long shots or dents). Thanks to an innovative lighting and camera concept, this inspection can be carried out without blind spots for any type of container opacity (opaque, translucent, transparent). Proven solutions are also combined with innovative approaches in the area of the container mouth. The well-proven inspection of the neck finish, which identifies typical defects in the injection molding process such as scratches and notches, is supplemented by special optics and lighting. The inside of the neck finish is inspected up to the level of the bottle neck in order to detect long shots and contamination inside the bottle as well.
The SpotWatcher also proves its versatility in the area of software extensions and peripherals. As part of the inspection of the outer bottle base, the reading of the cavity number of each container has been integrated into the range of functions. This data is then used to create a graphical evaluation of all inspection criteria depending on the cavities and to automatically monitor the defect rate of each cavity. An alarm can be triggered in the event of a defect sequence - but also at a certain percentage or nominal defect rate. The targeted ejection of all products from a defective cavity is of course also possible. The system also has a purely mechanical safety mechanism. If there is a fundamental error in the production process, which is reported by the blow molding machine or an operator, for example, all objects are ejected by means of a rejection gate.
If you would like to find out more about the versatile inspection options of the SpotWatcher Customized, please contact our sales team. We would like to thank the Sibo Group for their trust and are pleased to be able to make a contribution to quality assurance with the SpotWatcher Customized.