The closure inspection allrounders
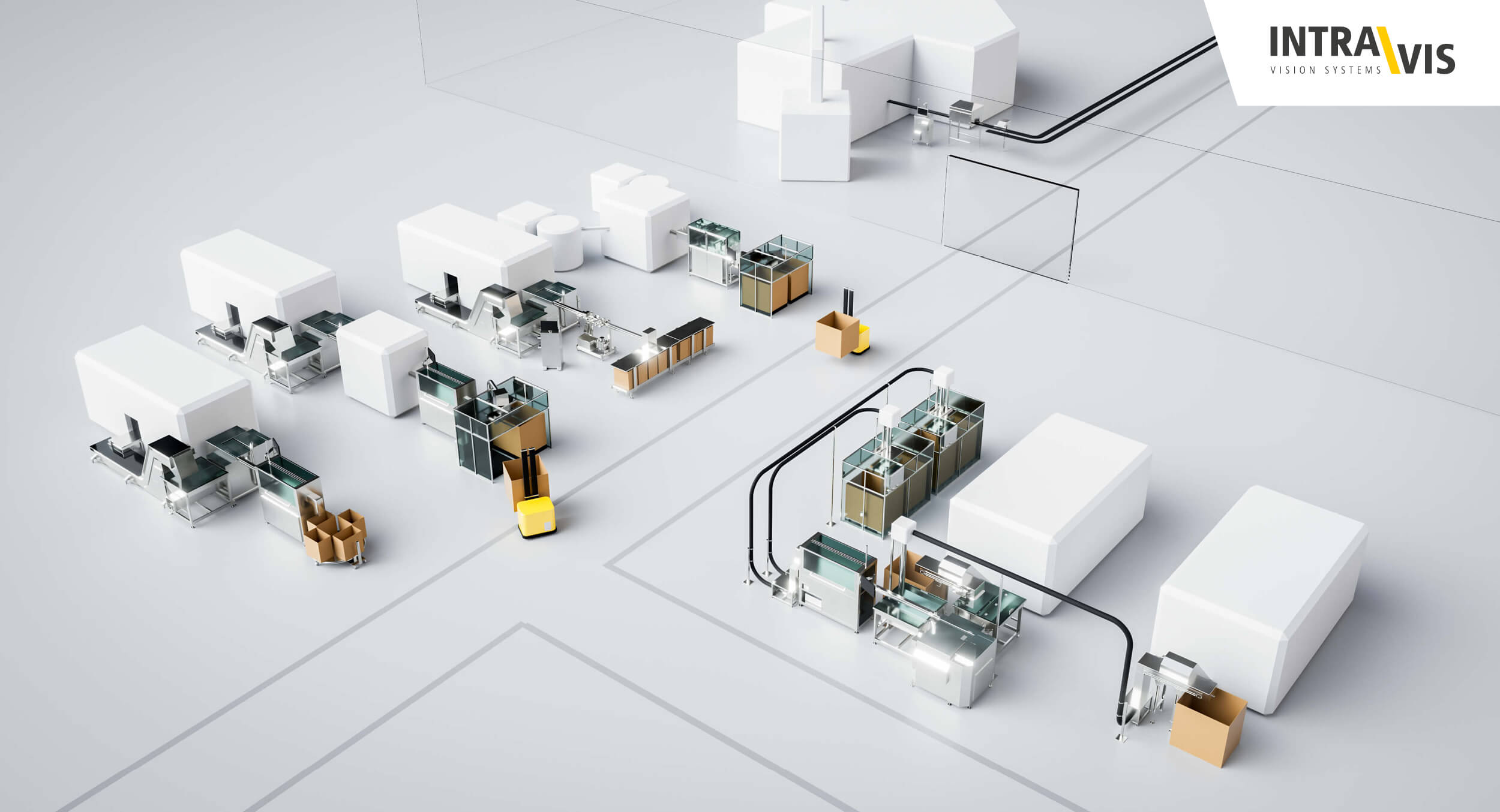
Solutions for the inspection of caps and closures of all kinds are among our core competencies. In the almost 30 years of our existence, we have accumulated a great deal of know-how and experience, which has led to a variety of different technologies for the inspection of all types of closures.
In the last decades, variations in closure designs have increased more and more. Nowadays, the market demands one-piece or multi-piece closures, sizes from 20 to more than 60 mm in diameter, with or without printing, slitted closures, flip-top closures, tethered caps and much more. To ensure high product quality, many closure manufacturers therefore use our systems to inspect their products. Because: This variety of closure design variants poses different challenges for inspection, which we can meet accordingly with our experience.
Standard closures
The term “standard closure” is deceptive. Even though these closures are standardized and therefore produced in large quantities, they also have important elements on which the producers of the closures put a special focus.
One priority of closure producers is, of course, the flawless functionality of the closures, especially in the thread area. Accordingly, one focus of our systems is on the comprehensive inspection of the thread - for example, with our CapWatcher Q-Line. Thanks to special imaging developed in-house, the entire thread is captured with one camera and then inspected for defects in a roll-out image.
Another crucial point in the production of standard closures is the closure dimensions. We use the CapWatcher Q-Line to inspect the external and internal dimensions, such as the height and diameter of the closure or even the diameter of internal sealing elements. Additionally, the CapWatcher Q-Line inspects the inside and outside of the closure for defects like contamination, color deviation and many more.
And we offer another technical highlight for the inspection of standard closures: our patented temperature sensor, which records the temperature of each individual closure produced. It presents essential data for the CapWatcher Q-Line. Based on the temperature information, conclusions can be drawn about the shrinkage behavior of the closures which allows for the implementation of a precise capping process. A closure manufacturer can ensure that the closure has exactly the dimension that is needed at the planned time of application. Additionally, the operator is able to monitor the cooling of individual cavities and ensure process stability.
The next essential element of closure functionality is a flawless tamper-evident band, which makes sure that a closure has not been opened already. Therefore, we have developed a technology to inspect the quality of the tamper-evident band. For slitted bands, additional attention is paid to the quality of the slit. For example, the technology inspects for deviations of the cutline or if the form is wavy. This makes it possible to detect worn knives or problems with the temperature of the blade at an early stage. Moreover, general defects like long and short shots or broken bridges are inspected at the tamper-evident band.
Multi-part closures
Standard one-piece closures are not only type requested by customers. With the increasing demand for sports drinks, other types of closures, such as push-pull or flip-top closures, have become popular on the market as well.
In terms of inspection requirements, these multi-part closures are more challenging than standard closures. The production of the closures is significantly more complex and creates several challenges such as protruding flaps, damaged pull tabs, special geometries, and assembly faults. Each individual element of the multi-part closure as well as the assembled closure must be inspected in order to be able to guarantee 100% safety.
To ensure this, we have a team of highly qualified mechanical, electrical and software engineers who develop the best inspection solution for each customer's individual needs and situation. Our managing director Dr. Gerd Fuhrmann likes to explain this in the following way: "With us, customers always receive a system developed and built specifically for their request. Of course, this is especially needed for projects with multi-part closures or even unusual dimensions of the closure. We rarely have any one project that is like the other, because every system and every order brings its challenges. Production line space is usually very limited. And sometimes special inspections have to be developed for a closure. With a standard solution, limits are quickly reached." In addition, we have been investing in a large service network for years in order to provide our customers with turnkey systems that are ready for operation after installation.
Tethered Caps
With the EU Directive 2019/904 Single Use Plastics (SUP), the need arose that caps are permanently connected to the bottle. As a result, this led to the development of an inspection solution for tethered caps. Even though these are similar to standard caps in many requirements, they do have some challenging elements, for example the CAMs located inside the closure. To avoid damaging them during micro-hole inspection, we invented our patented, non-contact HV inspection. As the name indicates, this inspection no longer dips into the closure during inspection to find micro-holes in the head plate of the closure.
The external shape and dimensional stability of tethered caps are further challenges that the inspection system must handle. Practice has shown that INTRAVIS’ form-fitting, patented lateral star wheel separation copes best with external features, such as hinges. Moreover, the separation technique precisely handles the high sensitivity of increasingly thinner closures even at the highest production speeds.
In addition, we use advanced software that can cope with any orientation of rotationally asymmetric closures like tethered caps. Specifically, this involves equipping individual modules with a new core algorithm based on Deep Learning. Marius Pötting, product manager for closure inspection systems, describes it this way: "The heart of our systems is the IntraVision, our self-developed software. It has been using Deep Learning algorithms for some time. As a result of our constant development efforts, we have succeeded in applying Deep Learning to the detection of anomalies.” Anomalies are any deviations from a pre-defined, optimal standard including deviations that are difficult for the customer to describe in advance.
The biggest advantage of this technology is the teaching process. Whereas previously a large number of samples were needed for each type of defect to be found, the new logic changes the approach completely. The software is first trained based on a pool of good parts, and thus learns how the optimal closure appearance looks like. This pool of good parts is necessary to evaluate natural variations as "OK parts" on the one hand, but also to evaluate small, real defects as "not OK parts" on the other hand. The quality of what has been learned is then checked and optimized based on bad part samples. In the subsequent real world production process, everything that does not correspond to this trained optimum is sorted out. By means of the adjustment options, the operator still has the possibility to influence the sensitivity of the inspection and, thus, the ratio between efficiency and object quality.
"The special feature of this software technology is its fast-learning capability. For example, if I teach the software with closures in different rotational positions, I do not need to align asymmetrical closures during inspection. And if I teach the system with other closure designs, it can also immediately inspect these as well,” says Marius Pötting, summarizing the possibilities of the technology.
Applied closures
Closures are naturally intended to be applied to filled bottles – and thus in the wet area of a production line. To enable our customers to use an INTRAVIS system in this area as well, we decided last year to develop a washdown design and the CapWatcher FC.
Marius Pötting mentions, "The CapWatcher FC is an INTRAVIS system developed exclusively for the wet area of the filling line behind the filler and capper. We have already been able to gain experience in the wet area in various projects over the past few years, which we have used and transferred to this stand-alone product." Based on this experience, the CapWatcher FC – both the inspection unit itself and the related electrical cabinet – is completely splash-proofed according to the IP65 standard as well as designed in accordance with the bottlers' hygienic measures. This makes cleaning the system easy and uncomplicated, even with aggressive methods and means.
One of the most important inspections in this area is the quality control of the application angle of the closure. With three side cameras, our CapWatcher FC uses index marks to inspect whether the closure is screwed down to its target position – or whether it is screwed down too far or not far enough. Marks on the closure and on the neck support ring that are barely perceptible to the end user are detected by the system. If these marks are within a tolerated range to each other, the system assumes that the closure has been completely and correctly applied – and the bottle is released for packaging. This new technology is used for the first time. Of particular interest to the production line operators are the comprehensive statistics that correlate the average application angle with the capping head. Thus, the operator can detect a malfunction of a capping head at short notice.
Summary
The variations of closures in their different application areas have steadily increased over the past decades. For this reason, it is all the more important that closure manufacturers have someone at their side in us who already has the right solution for every existing challenge and also has the ambition to master new challenges again and again. In doing so, we always work according to our vision: We solve problems. Before they arise.